Services
Plastic Bottle Products PET Technology in Pakistan
Plastix offers two-step technology of plastic bottle products and is a market leading company in PET Technology in Pakistan. Our key competence lies in satisfying all of our customers’ technical needs.
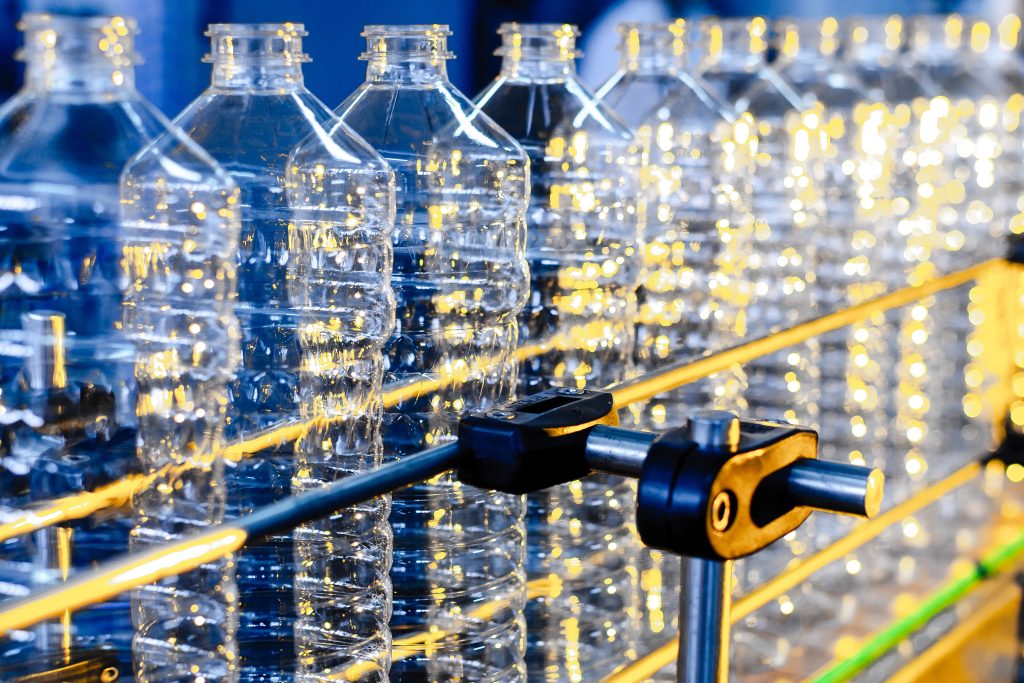
Plastix manufactures linear stretch blow molding Products with the output of up to 12.000 BPH. All the machines have excellent reputation thanks to their reliability, simplicity and high technological level. Plastix delivers complete manufacturing solutions including perform design and supply, bottle design, bottle moulds, perform loaders, ready bottle conveyor, air preparation and cooling system.
Pet Blow Molding Product
Plastix blow molding process can be controlled by controlling various parameters such as Temperature, Pressure, Stretch time, Stretch rate, Reheat time, Cooling time, clamping pressure and relations between these parameters. Temperature of perform for blow molding product is ranging from 90ºC to 110ºC. Temperature increases from bottom to top of perform. So that more material can move towards the bottom of the bottle during blowing stage. For pressure there are two phases one pre-blowing (Low air pressure 10 bar) and then final blowing (High pressure 40 bar). In pre-blowing stretch pin move forward and push perform and low air pressure (Pre-blowing). There should be synchronizing in stretch pin and pre-blow pressure. If the stretch pin is late than pre-blow pressure then there will be error in the bottom center and if high there will be tress whitening. The high pressure is applied so that perform take the shape of mold. High pressure is required to mark the detailed and sharp corner product.
Extrusion Blow Molding
In Extrusion Blow Molding (EBM), plastic is melted and extruded into a hollow tube (a parison). This parison is then captured by closing it into a cooled metal mold. Air is then blown into the parison, inflating it into the shape of the hollow bottle, container, or part. After the plastic has cooled sufficiently, the mold is opened and the part is ejected. Continuous and Intermittent are two variations of Extrusion Blow Molding. In Continuous Extrusion Blow Molding the parison is extruded continuously and the individual parts are cut off by a suitable knife. In Intermittent blow molding there are two processes: straight intermittent is similar to injection molding whereby the screw turns, then stops and pushes the melt out. With the accumulator method, an accumulator gathers melted plastic and when the previous mold has cooled and enough plastic has accumulated, a rod pushes the melted plastic and forms the parison. In this case the screw may turn continuously or intermittently. With continuous extrusion the weight of the parison drags the parison and makes calibrating the wall thickness difficult. The accumulator head or reciprocating screw methods use hydraulic systems to push the parison out quickly reducing the effect of the weight and allowing precise control over the wall thickness by adjusting the die gap with a parison programming device.
Injection Molding Product
The injection molding machine is based on an extruder barrel and screw assembly which melts the polymer. The molten polymer is fed into a manifold where it is injected through nozzles into a hollow, heated perform mould. The perform mould forms the external shape and is clamped around a mandrel (the core rod) which forms the internal shape of perform. The perform consists of a fully formed bottle/jar neck with a thick tube of polymer attached, which will form the body.
The perform mould opens and the core rod is rotated and clamped into the hollow, chilled blow mould. The core rod opens and allows compressed air into the perform, which inflates it to the finished article shape.